こんにちは。
スピーカー製作の続きですが、前回最後に書いた通り、厄介なことになってしまいました。言ってしまえば、設計ミスですね…板からできるだけ効率的に取ろうと苦心して試行錯誤を重ねていた最中、寸法を誤ってしまい気付かずスルーしてしまっていたわけです。ピッタリと板の寸法内に収まった(間違いだったわけだが)ので、浮かれてしまったのですね。よくよく見れば「あれ、これ短くね?」と気が付くような事なのに。これって「正常化バイアス」というヤツでしょうか、うまく行きそうな時ほど慎重にならねばなりませんね。まあ、これまでの長い自作経験から、トラブルが無かった事などありません。今回も華麗に切り抜けねば。
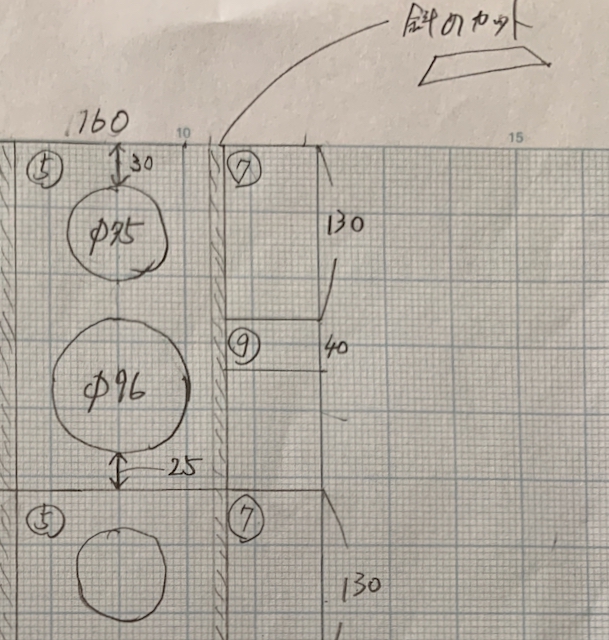
とりあえず、まだ足りないものの余った板を継ぎ足して「少しはマシ」という事で勘弁してもらおう(誰に?)。スリットダクトを形成するパーツとなる板には、クロスオーバーネットワークを搭載させるという重要な役割があるので、ある程度面積も要るのです。そんなわけで、板材の組み立てと同時にネットワークの構築です。コストダウンを目論み、使っていたものを最大限再利用しようとしたため、ローカットのコンデンサは3つを並列で用いる、という何とも面倒かつ場所を取る手法を採ってしまいました。合計が合っていれば問題はあるまい…

端子台もネットワークにはあると大変便利なアイテムです。いつもオーディオテクニカ製カーオーディオ用の金メッキ端子台を使っていますが、本当に使いやすいんですよね〜エンクロージャーの組み立ての方も粛々と進めていきます。小型で補強を入れたスリットダクト仕様のバスレフですから、それほど複雑なものではありません。対向面が非対称になるよう補強桟を入れながら、適宜吸音材を貼り付けます。吸音材には両面テープが貼られている厚手のフェルトと、押入れの中から発見されたアコースティックリバイブの天然シルク製吸音材。密閉型ではないので、吸音材は最低限で良いと思います。スピーカーターミナルはDayton製の安いけど高級に見えるしっかりしたもの。端子板は無いので、背面に直接装着させるしかありません。穴が緩くてもいけない…のだが、やってしもうた。ユルすぎたのでした。穴を空ける道具は自在錐というT字型の錐で2種類持っているのですが、これが帯に短し襷に長し。真ん中のサイズが欲しかった…もはやこういう道具はホームセンターにも無いのです。
(追記)残念ながら、現在は生産されていない模様です。
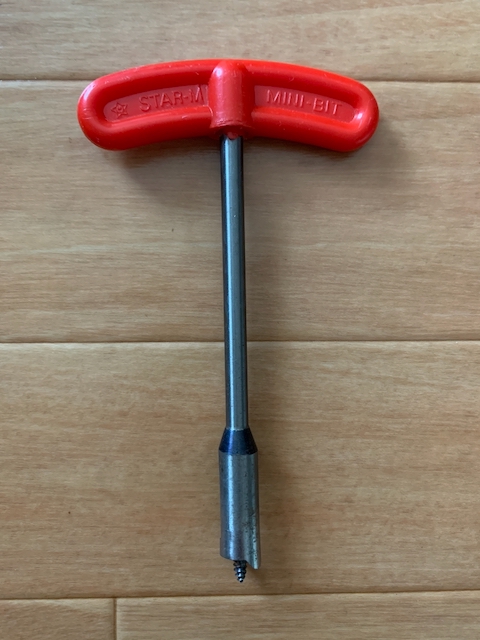
しかしAmazonで検索したら、あるじゃあないですか!早速ちょうどいいサイズをゲットできました。何故電動ドリルを使わないのか?マンション内で迷惑になる、という理由もありますが、自分自身が電動工具の音はどうにも苦手だからというのが大きいですね。音は良い音を聞きたい(笑)。
大きく開けてしまった穴は塞ぎ、再び新たに手に入れた自在錐で仕切り直し。今度はちょうど良く施工出来て満足でした。思わず長引きましたが。こういう時は、やっぱり端子板付きのものの方が便利ですね。
ここをクリア出来れば、あとは組み上げていくのみ。小さいので気は楽ですが、それでも接着面が浮いてくることはあるので、ハタガネの登場です。これでぐいぐい締め付けながら接合していきます。釘は使いません。ちなみに接着剤は「タイトボンド」を愛用しています。普通の「木工用ボンド」が音質面でのメリットが多いという話もよく聞きますが、何せ短気なもので…
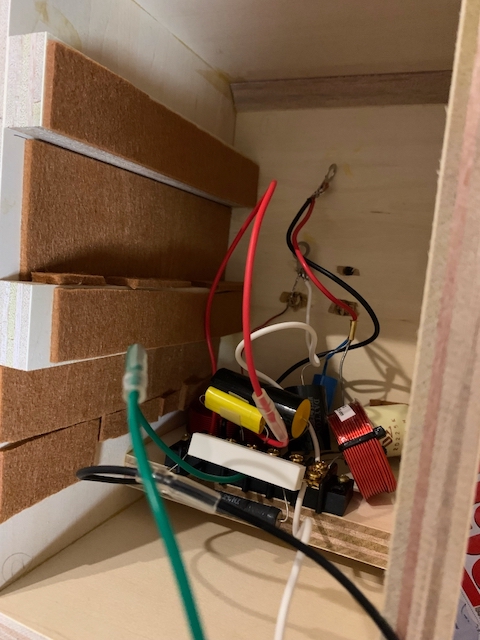
これで塗装を施せば、とりあえずはエンクロージャーは完成です。さて次は、いよいよ塗装編!長々と続け過ぎ、と言う声も聞かれそうですが、ごめんなさい、少々お付き合いをお願いいたします。
コメント